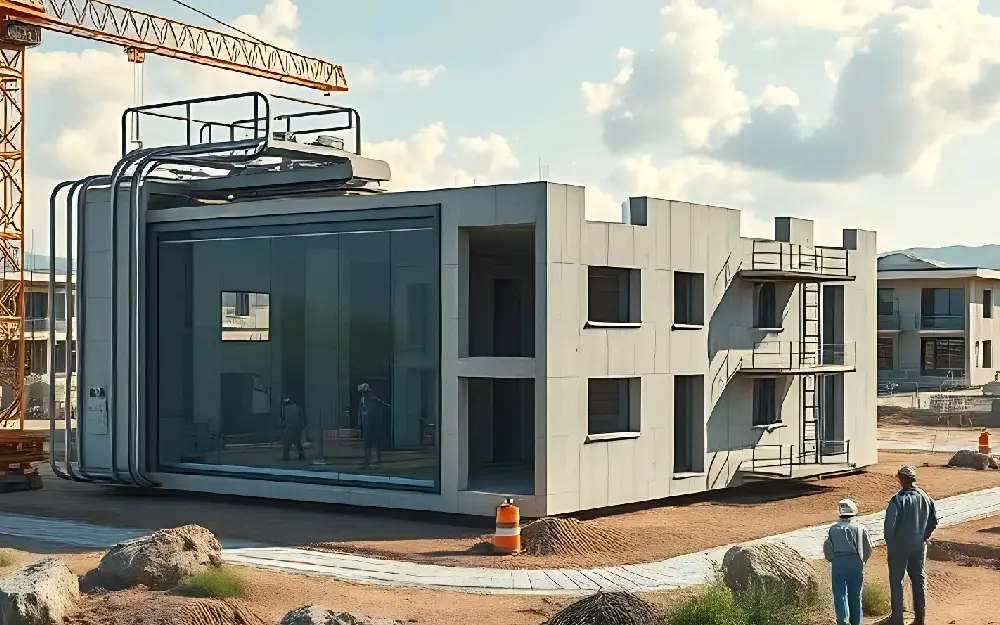
The Role of 3D-Printed Walls in Reducing Construction Costs
The construction industry has always been a pillar of economic growth, but it's also one that is known for being resource-intensive, expensive, and slow-moving in terms of innovation. However, in recent years, the introduction of 3D printing technology in construction has begun to revolutionize the industry, offering a significant reduction in both time and costs. One of the most promising advancements in this space is the use of 3D-printed walls, which is already making waves as a more affordable and efficient alternative to traditional building methods.
What Are 3D-Printed Walls?
At its core, 3D-printed walls are created using an additive manufacturing process, where a computer-controlled 3D printer lays down layers of material—typically concrete, cement, or specialized compounds—one by one to build up the structure. This contrasts with traditional construction methods, where materials are manually cut, shaped, and assembled by laborers. By using advanced printers, entire walls (or even entire buildings) can be printed directly onsite, reducing the need for labor-intensive activities and cutting down on materials waste.
1. Lower Labor Costs
One of the primary ways 3D-printed walls help reduce construction costs is by minimizing the need for manual labor. Traditional construction methods require teams of workers for tasks such as bricklaying, welding, and assembling different parts of a building’s structure. With 3D printing, much of the process is automated, meaning fewer workers are needed on-site for the same task. Not only does this reduce labor costs, but it also shortens the construction timeline, allowing projects to be completed faster.
Moreover, with automation taking over some of the most tedious and repetitive tasks, workers can be redirected to more complex, skilled roles that add value to the construction process. This can result in a more efficient allocation of human resources, further improving the overall cost-effectiveness of the project.
2. Material Efficiency
Another major benefit of 3D-printed walls is the precise control over material usage. Traditional building techniques often result in significant waste due to cutting materials down to size, which leaves behind scrap that may not be used. In contrast, 3D printing uses only the material necessary to construct the structure, resulting in minimal waste.
Additionally, the materials used in 3D printing are often designed to be more durable and sustainable. For instance, 3D printers can use low-cost, high-performance materials such as recycled concrete or eco-friendly composites, which further reduce material costs while contributing to sustainability goals.
3. Reduced Construction Time
3D printing is incredibly fast compared to traditional construction techniques. The process of printing walls can be done in a fraction of the time it would take for a team of workers to assemble the same walls manually. While a traditional construction project may take weeks or even months to complete, a 3D-printed home or building can be completed in just a few days, depending on the scale of the project.
This reduction in construction time not only cuts labor costs but also shortens the overall project timeline, meaning that the building can begin generating revenue (or fulfilling its intended purpose) sooner than conventional buildings. In fast-paced urban environments or in the case of emergency housing solutions, this rapid construction could be a game-changer.
4. Customization and Flexibility
One of the most innovative aspects of 3D-printed walls is their ability to be highly customizable. Using digital blueprints and 3D modeling software, designers can create walls with unique shapes, sizes, and features that would be challenging, if not impossible, to achieve with traditional construction techniques. This level of customization allows architects to design buildings that are both aesthetically pleasing and functional while reducing the need for costly custom labor or materials.
Furthermore, 3D printing makes it easier to adapt a project to different design preferences or building regulations. Because the walls are printed to precise specifications, adjustments can be made quickly and with less cost than modifying traditional construction plans.
5. Sustainability and Environmental Benefits
3D printing in construction isn't just about reducing costs—it's also about reducing the environmental impact of building projects. By optimizing material use and minimizing waste, 3D printing makes the construction process more sustainable. Plus, many companies are exploring eco-friendly materials, such as recycled plastics or sustainable concrete, for 3D printing, which further enhances the green credentials of the technology.
Additionally, since 3D-printed walls can be printed onsite, there is less transportation required, which cuts down on fuel consumption and reduces the carbon footprint of the project. This is particularly beneficial in urban areas where construction materials are often transported from distant locations, resulting in high levels of emissions.
6. Affordable Housing Solutions
One of the most exciting implications of 3D-printed walls is their potential to address the global housing crisis. The ability to rapidly construct affordable, sturdy homes at a fraction of the cost of traditional building methods has the potential to revolutionize the way we think about housing. In regions facing housing shortages or in disaster-stricken areas, 3D printing could offer a swift, affordable solution for creating homes and shelters.
By dramatically reducing the cost of construction, 3D-printed homes could be made available to a wider range of people, including those in low-income or underserved communities, providing them with access to safe, quality housing.
7. Long-Term Cost Savings
While the initial investment in 3D printing technology may seem significant, the long-term cost savings it provides are undeniable. The reduction in labor costs, material waste, and construction time can result in substantial savings over the life of a project. Additionally, 3D-printed homes often require less maintenance over time due to the durability and energy efficiency of the materials used.
Furthermore, because 3D printing can be used for a wide variety of structures—ranging from residential homes to commercial buildings and even bridges—the versatility of this technology ensures that it will continue to reduce costs in many different areas of construction.
Conclusion
The use of 3D-printed walls in construction is an exciting development that promises to reduce costs, increase efficiency, and provide sustainable solutions for the housing and construction industries. As the technology continues to evolve, we can expect even greater innovations that further cut costs while improving the quality and accessibility of buildings. In a world where construction costs are continually rising, 3D printing could be the key to unlocking a more affordable and sustainable future.